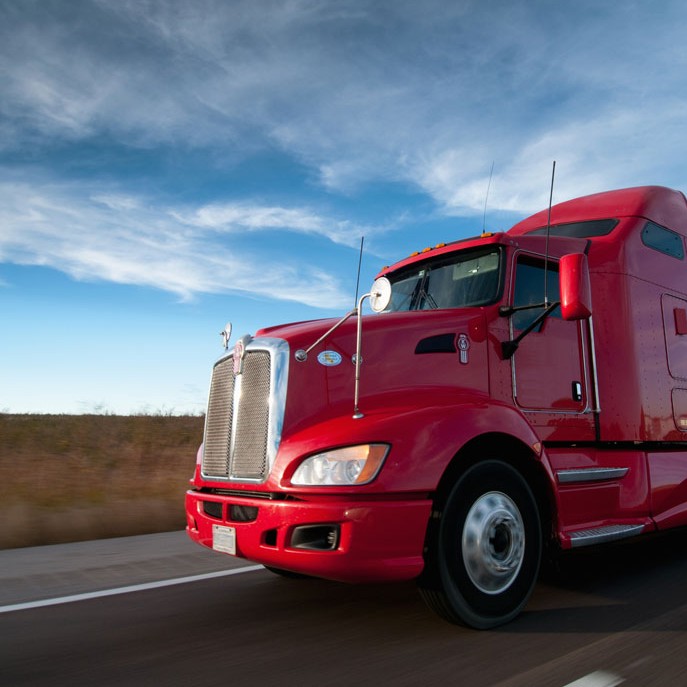
Truck
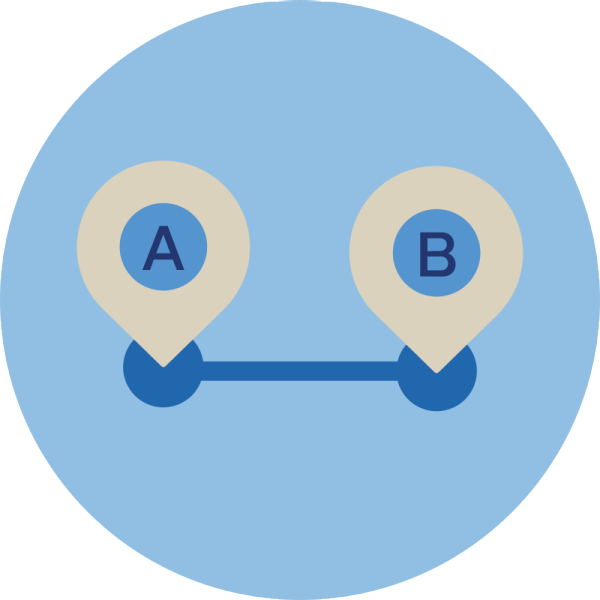
Business and Journey Risk Factors
The area that a truck driver operates in, the distance travelled within that area and the frequency of those trips, have a direct impact upon the exposure to incidents. Long distance haulage is more likely to increase the risk of fatigue, whilst frequent repeated trips over a short distance will allow the driver to be familiar with inherent aspects of the roads used, providing complacency doesn’t set in.
What do we look for?
Negative
- Long haul trips.
- Any delivery trips that are a ‘one-off’ or are conducted infrequently.
Positive
- Frequent trips over local familiar routes.
- Same drivers are used on infrequent, medium or long haul trips.
- No productivity or time constraints imposed upon drivers.
Risk improvement ideas
- Try to minimise productivity or time constraints on drivers, even for short haul frequent trips.
- Ensure that medium, long and infrequent trips are suitably planned.
- Consider using the same driver and truck for frequent medium and long haul trips so that they are familiar with the route, scheduled stops and rest areas.
Two major factors influence this risk area. The most obvious is high hazard dangerous goods (e.g. poisons, explosives). The second risk is the less obvious load stability factor. A major contributing factor to high value roll-over/tip-over crashes can often be traced to the instability of loads.
What do we look for?
Negative
- High % of dangerous goods hauled.
- Low % of dangerous goods hauled but employees not properly trained.
- Delivery of bulk material in unstable ground.
- Intermodal containers or any shipping vehicle NOT loaded under the control of the transporting company.
Positive
- Palletized goods in a rigid trailer.
- Best Practice hazardous transport training for all employees.
- All freight is consolidated at a transport facility by company employees
Risk improvement ideas
- All dangerous goods involved in the transport, handling, or administration of loads must receive best practice training that includes a minimum of material identification (UN standard), safe handling instruction, initial emergency response, and shipping paper instructions.
- Equip all vehicles with blocking and bracing tools to stabilize loads.
- Use only experience drivers to deliver dump/tipper loads in areas with other than hard surfaces. Experienced driver will understand the inherent tip-over risk associated with the rising centre of gravity on unstable ground.
The accumulation of significant concentrated asset values in a fleet indicates the potential for a severe single event loss, such as a depot fire, or major collision. The concentration of vehicles may be static (e.g. in depots, workshops) or dynamic (e.g. a multi-trailer combination transporting valuable cargo).
What do we look for?
Negative
- Congested single parking area for vehicles parked at depots / workshops.
- Minimal spacing (1-2m) between vehicles parked at depots / workshops that will enable prompt fire spread from vehicle to vehicle.
- Multi-trailer combinations with valuable cargo.
- Vehicles with specialised fittings, exterior finishes, upgrades, etc.
Positive
- Multiple clusters of vehicles parked in a spacious, secured depot / workshop.
- Good spacing (3m+) between vehicles parked at depots / workshops that will delay fire spread from vehicle to vehicle.
- Simple, standard value, dynamic vehicle combinations.
- Minimal specialised fittings, exterior finishes, upgrades, etc.
Risk improvement ideas
- Try to provide at least 3m spacing between each vehicle parked at depots / workshops.
- Try to park vehicles in multiple clusters (rather one large single group) with 15m+ spacing between each cluster.
- All vehicles parked indoors, should be located in buildings that are fitted with remote monitored sprinkler / fire detection systems.
In order to adequately manage driver fatigue in your operations, you should first establish the level of work related fatigue exposure for your drivers. Two good indicators as to the level of work related fatigue exposure are;
- the extent and type of work conducted during overnight hours
- the extent and type of shift / roster changes or rotations.
What do we look for?
Negative
- A high volume of overnight work.
- Many drivers that drive right through the night.
- A lot of ‘on-call’ work with unpredictable driving hours.
- Extensive and / or erratic shift / roster rotations.
Positive
- Negligible overnight work.
- If significant overnight work then the journey is broken up with breaks.
- Fixed morning, day, afternoon or night shifts / rosters.
- Negligible ‘on-call’ work – predictable driving hours.
Risk improvement ideas
- Whilst the customer demands may be variable, remove this variability from the work patterns for drivers (ie. so that they come to work at the same time on the same days of the week and do tasks / jobs / routes that they are highly familiar with).
- Try to minimise the volume of overnight work. If overnight night work is necessary then consider higher levels of controls for fatigue.
- If trips that travel right through the night are necessary then try to break up the trip by implementing driver changeover points (and enable drivers to sleep in their home bed).
- Aim at fixed shifts / rosters for drivers (to enable them to acclimatise to their work patterns) and have the time of day for the shift in mind when recruiting new drivers for positions. Try to select new drivers that have months / years of experience of working these required hours.
Resources
The types of roads driven on, terrain, congestion and adverse weather conditions can have a significant contribution to crashes. It is important that drivers recognise these changing conditions, or road types, and adjust their driving technique accordingly. Training and instruction may play an important part in increasing drivers’ awareness of these hazards.
What do we look for?
Negative
- Significant driving in adverse weather conditions.
- Regions that have rapidly changing weather conditions, including storms, snowfall, rainfall, bright sunshine etc.
- Remote or rural areas where road surface conditions are poor.
- Drivers who may be exposed to a wide variety of road types, surfaces and congestion.
Positive
- Regular route assessment and/or planning.
- Specialised driver training.
- Ensuring vehicles are adequate for road and weather conditions.
- Ensure that drivers are equipped with additional safety equipment (eg, snow chains, shovels for snow; or daytime running lights for bright sunshine).
Risk improvement ideas
- Where adverse terrain, road types, road surfaces etc exist, consider implementing procedures to plan routes.
- Consider specific training for drivers in adverse conditions, such as unsealed roads, off-road driving etc.
- Consider training and awareness programs for drivers who may experience adverse, or rapidly changing weather conditions.
Resources
Protection against fire, theft and vandalism, both on premises when parked and when vehicles are being used or operated off site is a vitally important factor. However what is often overlooked is the need to provide drivers/staff with extensive training in fire/theft prevention, use of fire extinguishers and appropriate firefighting techniques.
What do we look for?
Negative
- Significant fire hazard presented by proximity to either hazardous or combustible materials.
- No Fire Department available, or response time is in excess of 15 minutes.
- Prompt removal of vehicles in the event of fire is difficult and/or vehicles are parked unattended on a public street.
- No security provided e.g. premises are unfenced, have no gate or are unlit.
- High concentration of equipment / values at one location.
- High frequency of prior theft loss activity.
Positive
- No previous fire, theft or vandalism losses on risk.
- Fire Department response time is less that five minutes.
- Adequate water supply (hydrants) on-site. On site security provided 24/7.
- Staff have received extensive training in fire prevention, safety procedures in the event of fire and/or fire fighting.
- Vehicles are equipped with satellite tracking and/or recovery units. Regular inspection & maintenance of these units by a certified contractor.
Risk improvement ideas
- Ensure that assigned parking areas are not in proximity to storage or manufacture of dangerous and/or combustible materials.
- Develop emergency procedures for fire response and ensure that all drivers/staff have received appropriate training. This should also address fire/theft prevention techniques, use of fire extinguishers and appropriate fire fighting techniques.
- Equip vehicles with satellite tracking/recovery units and ensure that regular inspection & maintenance of the units is provided.
- Designated on-site parking areas should be fenced, gated and manned by 24/7 security.
- Best practice requires that premises are protected by suitable security e.g. fence, gate, 24/7 guards and prompt Fire Department response time in the event of fire.
This is an inherited exposure from such activities as pulling trailers that are owned by others or conversely, where owned trailers are pulled by other carriers. In addition, carriers must be aware of inheriting exposure should they use shipping documents generated by another party e.g. a shipper, manufacturer or another carrier who has a contractual agreement with a shipper or manufacturer. In such cases, without the protection of your own Bill of Lading, contractual obligations placed on others can be transferred.
What do we look for?
Negative
- Rental/Lease of equipment without purchasing insurance when Zurich’s policy excludes short term or daily rental.
- Uncontrolled fleet procedures to be aware of opportunities to use a Company vehicle for others (moonlighting).
- Using sub-contractors who have insufficient third party insurance coverage.
- Allowing passengers (non employees) to be carried.
Positive
- Audit and ongoing monitoring of vehicle use procedures.
- Active risk assessment to allow proactive action aimed at avoidance of these types of inherited exposures.
- Company policies ensure that all subcontractors provide proof of adequate insurance.
- Provide training to staff to ensure understanding of Company policies.
Risk improvement ideas
- Company procedures must extend to include such things as personal use and passenger policies.
- Establish a procedure which requires that any sub-contractor, driver agency, or casual drivers are required to have in place adequate insurance coverage i.e. at least equal to your own insurance coverage and limits, and that documentary proof of insurance is received prior to any work being assigned, as well as monitored on an ongoing basis to ensure that coverage(s) are current,
- The Company is aware of any Hold Harmless agreements that may exist which could create an obligation for acceptance of vicarious liability.
- Risk Management activities address all areas of operations to ensure that Vicarious Liabilities are recognized and obviated.
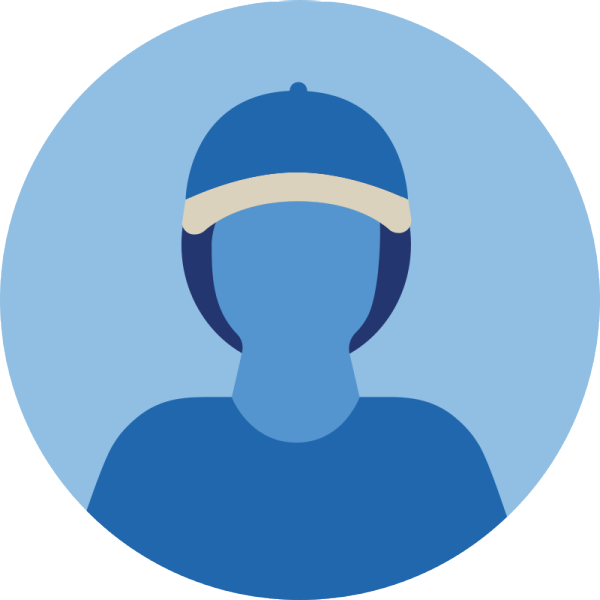
Driver Risk Factors
We all assume that we can drive well, but it a skill that is learned through training and experience. Unfortunately, if ongoing training is neglected, we may also develop bad habits in our driving skills.
It is important that the attitude and levels of hazard perception, behaviour and driving knowledge are assessed for all drivers so that the extent of on-road and awareness training required for the driver can be determined.
What do we look for?
Negative
- No formal assessment of drivers with regards to driving awareness or on-road skills.
- Lack of of inherent risks that require specialised training for drivers who are deemed to be a “high risk”.
- No recognition training, such as remote working, unsealed road driving etc.
- Lack of mentoring / buddy system training for first few days / weeks of employment.
Positive
- Formal recruitment procedures that include computer-based, classroom, written and/or on-road assessment of an employees driving awareness and skills.
- On-going/Periodic reviews of driving awareness and skills for all drivers – based either on collision history or time period.
- Formal training programs – at least for increased risk drivers.
Risk improvement ideas
- Establish formal driver assessment programs as part of the driver selection process and on an on-going basis (i.e. either periodically or based on collision performance).
- Ensure all new drivers undergo mentoring / buddy system training (i.e. direct driving supervision by an experienced senior driver), if not formal on-road training, for the first few days / weeks of employment.
- Provide driver training (i.e. at least driver awareness training if not formal on-road training) for those drivers that have been identified as ‘Increased Risk’.
- Provide ongoing ‘refresher’ training in driver awareness and / or on-road skills for all drivers (i.e. either periodically or based on collision performance).
Resources
Regular contact between employees and management helps ensure that the driver and the vehicle are monitored often. This helps assess the condition of the vehicle, signs of damage etc, whilst also promoting good management inter-action with the drivers to assess their well-being, productivity and demeanor. Regular contact with drivers can be direct – eg, visually, or by telephone/radio; or indirect – eg, via GPS.
What do we look for?
Negative
- Drivers are involved with long-distance routes or work away from the depot for prolonged periods.
- Management are not keen to make routine contact with drivers.
- Isolated depots are used where there is no management presence.
Positive
- Management ensure that there is regular contact with drivers when at the depot.
- When drivers are away from the depot for a prolonged period, there is frequent contact with management by telecommunications.
- ‘Buddy’ radio system among drivers.
Risk improvement ideas
- Ensure that long-haul drivers are spoken to by management when they return to depots. This promotes well-being and value. At the same time it ensures that drivers and vehicles are periodically ‘examined’ by management.
- Hold periodic driver – supervisor communication workshops or team meetings.
- Where long periods away from depots are inevitable, consider regular point-to-point contact via radio or telephone.
- Involve management of destination depots to be in contact with drivers.
- Also consider the merits of GPS technology and other on-board data management systems that monitor the driving ‘style’ of drivers, interaction with the truck etc.
With the on-going worldwide driver shortage, many firms find a rich resource pool of driver candidates in the rapidly maturing workforce. Driving often makes the perfect “second” occupation. However, consideration must be given to aging impairments such as slowing motor skills, reduced night vision, reduced hazard perception and lower stamina levels.
Youthful drivers may also be an attractive resource for filling driver needs. Although youthful drivers may not have the same limitation listed for mature drivers their overall lack of driving experience as well as experience in heavy duty vehicles dramatically increases the exposure to crash involvement.
What do we look for?
Negative
- Young drivers with two years or less experience in heavy duty vehicles.
- Like young drivers, “second career” mature drivers may lack experience in certain types of vehicles.
- No ongoing (or too infrequent) monitoring of driver health (other than pre-employment medical examinations).
- Inadequate scope of medical examinations (e.g. only evaluate hearing or eyesight).
Positive
- Wellness programs are part of the risk management strategy.
- Driver training takes age and skill level into account.
- Medical examinations are conducted by a medical practitioner (or nurse practitioner) and cover hearing, eyesight, blood pressure / cardiograph and blood analysis (diabetes, cholesterol, drug and alcohol).
Risk improvement ideas
- Structure your medical examination program so that all drivers are tested at least every 1 - 2 years with annual tests for mature age drivers or those with pre-existing ailments.
- Ensure that medical examinations are conducted by a company appointed medical practitioner (or nurse practitioner) and cover hearing, eyesight, blood pressure / cardiograph and blood analysis (diabetes, cholesterol, drug and alcohol) as a minimum.
- Provide an active health management program (e.g. ongoing education on nutrition and exercise) for all employees.
- Frequent proactive measures such as medical checks, eye exams and training to designed to help drivers recognize and overcome limitations is essential to control losses from a maturing workforce.
Full-time permanent drivers, if selected correctly, have greater levels of company loyalty than casual or seasonal drivers, who often are only interested in earning a wage for a period and moving on. The more ‘relaxed’ attitude often associated with seasonal or casual staff often translates into more frequent crashes. Self-employed drivers who operate their own trucks and are offered frequent or long-term contracts are highly regarded too, as they have sufficient business incentives to avoid crashes.
What do we look for?
Negative
- Significant dependence upon casual drivers, recruited for short term periods and required to drive company owned trucks.
- Seasonal fluctuations in business operations requires the need for additional drivers for short term periods only.
- Full-time permanent drivers make up less than 70% of driving workforce.
Positive
- Majority of drivers are full-time employees.
- Contracted drivers are used, but only Owner Operators.
- Owner Operators are selected using the same criteria as permanent employees (eg, frequent, long-standing contract).
- When recruiting Owner Operators, the same standards of selection are used as for Full-time Permanent Drivers.
Risk improvement ideas
- Try to avoid relying upon short-term labour only hired in drivers, unless it is necessary for holiday and sick leave cover. Try to use an established Driver Hire Agency, and assess their own internal selection and assessment/management procedures that are similar to your own high standards.
- Assess local Owner Operators, and utilise them to fill in for temporary gaps in your workforce. Try to use the same levels of selection criteria that you would use if employing drivers full-time.
There is a saying in the fleet business that you hire your next loss. Without strict driver qualification and selection standards fleet risk management efforts will fail.
Qualifications standards must consider age, past driving history, experience, ability and medical reviews to be effective. Selection must be tightly governed with the goal of hiring only the best.
What do we look for?
Negative
- Minimum Qualifications do not include age, past driving history (violations or road rules and past crashes), experience in similar vehicles, abilities to work efficiently and safely.
- Qualifications Qualifications are not applied uniformly.
- There is no formal review of each new hire by company officials.
- No driving test is given prior to employment.
Positive
- Each candidate is reviewed by one or more management personnel.
- Qualifications are published and periodically reviewed with hiring staff.
- No deviations from the qualifications standards is tolerated.
- Drug testing is included in the qualification standards.
Risk improvement ideas
- Publish written qualification standards that include:
- Minimum age
- Minimum experience level in like type of vehicle
- No more than three(3) minor road rule violations if the past five years
- No serious (drink driving, reckless driving, etc) road rules violations in the past five(5) years
- No more than one(1) on-road crash in the past three years
- Display driving ability during on-road test given by pre-qualified company personnel
- Satisfactorily complete pre-employment aptitude/behavioural driver assessment
- Pass medical examinations.
- Establish procedures that require at least one upper level manager to review, agree and sign-off on the field supervisors decision to hire
Conditions that lead to voluntary and involuntary replacement of drivers (turnover) creates exposure to possible losses from many areas. For the most part, newer employees spend more time concentrating on procedures to get the job accomplished and less time on proper defensive driving. Unfamiliar routes and vehicles also detract from the driving task.
There are many factors that lead to turnover but working conditions and wages are the main factors.
What do we look for?
Negative
- Drivers have no input in matters that effect their daily job including route planning, vehicle specifications, load configuration and length of working day.
- Vehicles are not suited to the task – poor maintenance.
- Wages are below regional average or are production based.
- Driver does not feel comfortable with the job due to lack of training/mentoring.
Positive
- Organisation has developed procedures to incorporate driver in the management process including daily planning.
- Pay and benefits package are above regional/national averages to attract top performers.
- Maintenance program is proactive.
- Work routine is attractive. Vehicles specifications are comfortable and adequate for the tasks.
Risk improvement ideas
- There are no magic programs to improve this risk factor. Your organisation must be prepared to support the frontline driver with all the tools and programs necessary for them to perform at a high safety level. Use the simple “boardroom” test to determine if your driver programs are adequate to reduce turnover. If you would not feel comfortable asking a member of the board or top management to drive the vehicle, work the hours or except the pay - then you should not ask your driver to find it acceptable.
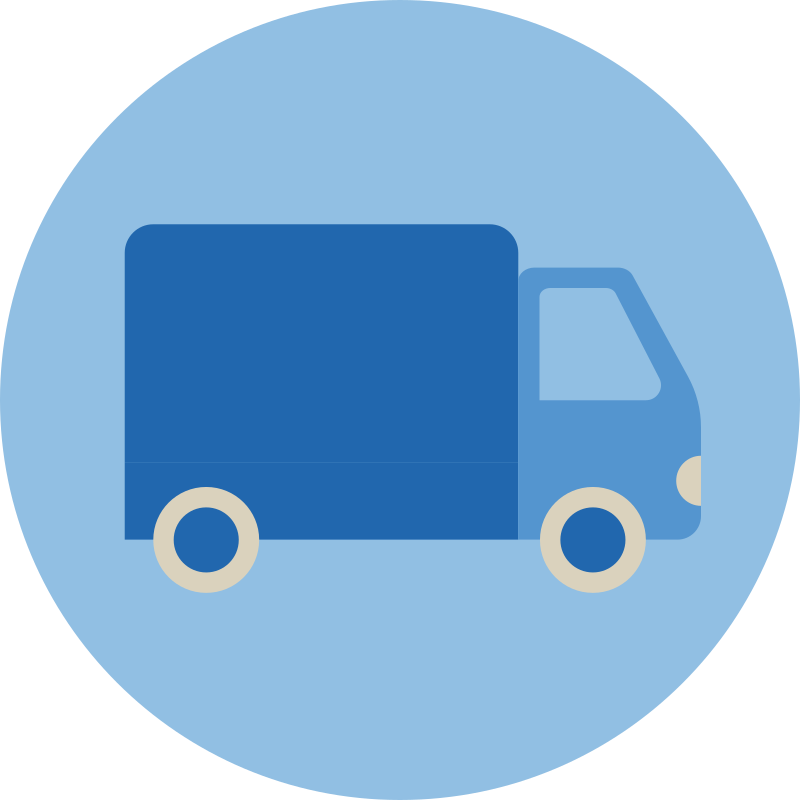
Vehicle Risk Factors
Employers are responsible to ensure a safe work environment for their employees. Motor fleet owners face additional challenges to ensure that vehicle specifications recognize safety features for both drivers and equipment. Therefore consideration is needed for proper engine, suspension and carrying capacity of equipment, as well as job task, employee safety, ergonomics, load securement, speed limiters, anti-jack-knife devices, stability control, fire-fighting appliances, ABS, suitable mirrors and so on.
What do we look for?
Negative
- Minimal or no safety features are provided, except where they are fitted as standard by a manufacturer during the manufacturing process.
- Any safety features provided have been determined without risk assessment and are included on economic grounds only.
- Some safety features may have been provided but training of staff has not been given and the “safety culture” does not recognize employee safety.
- The carrier has specified features which are unsuitable for current operations.
Positive
- Safety features in vehicles have been determined through a risk assessment process.
- All safety equipment is inspected (and documented) at least on a monthly basis and are included in the carriers inspection and maintenance programme.
- All drivers/employees have received training in the use and capabilities of all safety equipment.
- Policies are monitored and reviewed as part of the Safety Management process.
Risk improvement ideas
- Decisions on safety features should include vehicle protection, employee safety and welfare, and protection or reduction of their liabilities.
- Fleet acquisition/procurement standards should address vehicle and employee safety features.
- All aspects of the carrier’s operations and the individual job tasks should be fully evaluated (risk assessed) and decisions on what safety features to be selected should be based on those findings.
Carriers must be aware of the specific demands on vehicles and equipment associated with the nature of their business. This will allow them to develop vehicle selection and specification standards and to assess the optimum time for vehicle replacement. All vehicles reach a time when the cost of maintenance, repair and continuing use exceeds the performance and return. Before reaching that time, the carrier should develop a programme of phased replacement which considers vehicle age. model and specification and which will allow for the best resale, optimization of operating cost, and return on initial investment.
What do we look for?
Negative
- No vehicle replacement programme (vehicles may be “run into the ground” until they are incapable of being used).
- Vehicles are replaced after a number of model years and there is no consideration for very high mileage.
- Contract operators are not subject to any vehicle age standard or replacement requirements.
- Vehicle replacement is based only on cost considerations and does not consider job requirement specifications.
Positive
- A risk-based replacement process exists which considers operating needs and tasks.
- Replacement considers both vehicle age and degree of use (mileage) and is able to recognize excessive use.
- Replacement programme includes all power units, trailers and attached equipment.
Risk improvement ideas
- Develop risk-based replacement programme which determines replacement cycle and specifications via assessment of operational needs and tasks.
- Programme must be linked to other activities, such as maintenance, in order to have awareness of operating costs and allow for cost optimization and resale values
- Replacement programme must be continually monitored and reviewed in order to recognize changing job requirements.
- Replacement programme should include not only power units, but also extend to include trailers, attached equipment such as cranes, lift trucks, refrigeration equipment, etc., and any other specialized equipment need in operations.
- Where older model vehicles are in use, best practice maintenance programmes could include continual rebuild of existing equipment. In such cases, the fleet owner will know more about the condition of the vehicles than anyone else.
There is no mystery about it; poor vehicle maintenance leads to crashes, equipment failure and escalating maintenance costs. Most fleet operators are aware of the need to conduct routine maintenance, but the frequency of this is often dictated by weather/road conditions, types of goods carried, environmental conditions, journeys etc. In some regions, the condition and maintenance of vehicles is a legislated requirement. Having a program in place to ensure that trucks and trailers are routinely inspected, (and faults reported) will quickly highlight necessary repairs.
What do we look for?
Negative
- Maintenance of trucks and trailers relies exclusively upon the diligence of drivers and/or shows indications of “crisis” maintenance.
- No programme of regular preventive maintenance exists.
- Frequent vehicle breakdowns.
- A programme may exist but is is poorly documented and cannot evidence regular maintenance.
Positive
- A policy exists that requires all drivers to carry out regular (daily) vehicle inspection/check.
- All vehicles are serviced by manufacturer approved contractors in line with required intervals.
- Maintenance documents are complete and audited to ensure compliance with the corporate maintenance programme.
- Where maintenance is performed in-house, all staff are qualified to perform and are trained on maintenance programme requirements.
Risk improvement ideas
- Develop a documented Preventative Maintenance programme which addresses all vehicles, trailers and attached equipment e.g. boom cranes, reefer units, etc, and contains standards and frequencies for regular inspection, service and other maintenance.
- The programme must include requirements for regular review/audit of all documentation to ensure the Policy is being adhered to.
- Training has been provided to all drivers, maintenance staff and dispatchers to ensure that all understand their responsibilities under the programme. The training process should be fully documented.
- Consider establishing Condition Reports, completed by in-house mechanical technicians when vehicles are in for service. This is particularly useful in fleet operations where vehicles are exposed to a higher degree of “wear and tear” e.g. dump trucks, flatbed carriers, etc.
Theft of vehicles and of contents of vehicles can be expensive, time consuming, cause disruption of normal business activities and jeopardize relationships with customers.. Similarly, malicious damage to vehicles can often prove to be expensive, particularly if your company has a high insurance excess. Consideration should also be given to theft target commodities being carried as this often results in loss and/or damage to equipment.
What do we look for?
Negative
- Vehicle purchasing/specification policies do not take into account the risk of theft and fail to include anti-theft alarm capability.
- Attractive (theft target) cargos are frequently/regularly carried.
- Terminals have inadequate parking and/or security measures.
- Significant numbers of vehicles are operated and/or are parked in known high crime rate areas.
Positive
- Consideration of factory fitted and retrospectively fitted security devices when ordering company vehicles.
- Specific Vehicle Security Management Policies and Procedures exist.
- Good security arrangements at all company terminals.
- Procedures provide guidance to drivers on use of secure parking arrangements/facilities while en route.
Risk improvement ideas
- Perform an assessment of theft risks associated with fleet activities, areas of operation, commodities being carried and vehicle specifications
- Establish appropriate Security Management Policies after completion of an assessment theft risks
- Consider including anti-theft devices in Company vehicle specification/purchasing standards
- Company policies provide guidelines to drivers regarding safe and secure parking when en route and when parking at home.
Resources
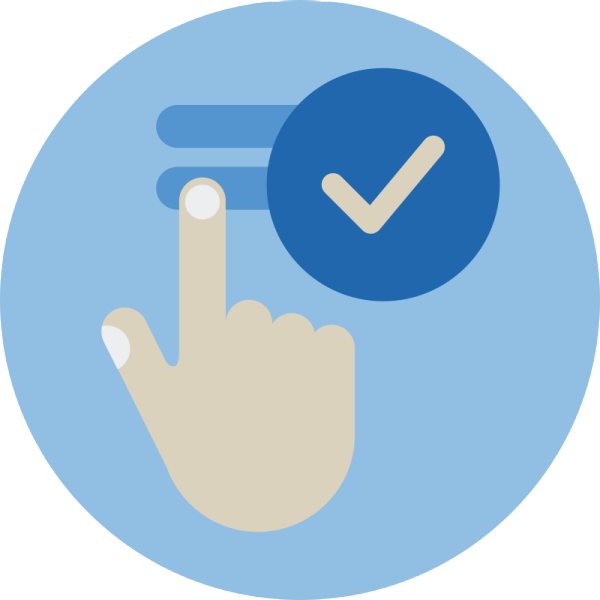
Management Controls
Drug and alcohol use amongst the population is quite common. Hence, you may be naïve to think that some of your drivers do not partake in the use of illicit / prescription drugs and alcohol.
The impairment of driving performance associated with drugs and alcohol is well documented and can be severe resulting in fatal consequences.
What do we look for?
Negative
- Failure to test for drugs and alcohol during driver selection.
- An acceptance that drug and alcohol issues may exist but there is sole reliance on random, on-road Roads Authority / Police testing for detection.
- No drug and alcohol policy.
- The drug and alcohol policy fails to address the effects of prescription drugs.
Positive
- Pre-employment drug and alcohol testing is mandated for all new drivers.
- Specific A drug and alcohol policy exists and is formally communicated to all drivers as they commence and on an ongoing basis.
- Random, ongoing drug and alcohol testing is mandated for al drivers.
- A substance abuse program is established with avenues for driver support.
Risk improvement ideas
- Ensure that pre-employment, random ongoing and post collision drug and alcohol testing for all drivers is ‘a way of life’.
- Ensure that a drug and alcohol policy is communicated to all drivers at induction and clearly details unacceptable behaviour / consumption and disciplinary measures along with any support services.
- Establish support services (i.e. a substance abuse program) with an appropriate medical practitioner / counsellor for good performing drivers that may declare their drug / alcohol issues in a bid for help.
Resources
In order to adequately risk manage fatigue related hazards, rosters / schedules, fatigue monitoring and training programs need to address both ‘work related’ and ‘away from work’ fatigue issues.
The greater the fatigue exposure in your operations, the more comprehensive and ‘risk based’ these fatigue controls will need to be.
What do we look for?
Negative
- Only reactive fatigue controls established that typically follow legislative compliance or major loss.
- Lacking or poor systems established for either continuously or periodically monitoring fatigue in drivers.
- Very little training / information on fatigue provided for drivers.
- Little consideration for everyday aspects of fatigue such as returning from leave and sleep apnoea.
Positive
- Proactive fatigue controls are established in advance of legislative compliance or major loss.
- Fatigue training programs are formally established and applied consistently across all operations of the organisation.
- Fatigue monitoring systems are established and applied consistently across all operations of the organisation.
- Drivers returning from leave or suffering from sleep apnoea are identified and managed.
Risk improvement ideas
- Do not rely on legislative compliance for adequate risk management of fatigue.
- Rosters / schedules for drivers should maximise the opportunity for night-time sleep at home for drivers.
- Ensure that hours of work (driving) are reviewed at least periodically (less frequently for reduced fatigue exposures and more frequently for increased fatigue exposures) and include analysis / awareness of individual daily and weekly work / rest periods with trigger points established for increased controls at maximum acceptable work durations (e.g. more breaks or simpler tasks at extended hours). Consideration should also be given to away from work / quality of sleep aspects. This may require a comprehensive Risk-based Integrated Fatigue Management program (RIFM).
- Fatigue training programs should be provided (especially for increased exposure drivers) that suitably cover time of day, duration of work, sleep quality, health, diet, social rhythms, etc – they should not merely focus on the work aspects of fatigue.
Resources
Many companies monitor business operating performance, profitability, accountability and are comfortable with setting business targets. More progressive organisations will include safety performance as part of their business monitoring. What is less common is businesses transcending these ideals to include the safety, performance and fiscal accountability of the fleet. Fleet Performance Management involves a number of risk management techniques and procedures, including Loss Reduction Targets, Incident Investigations, Analysis of incidents data and statistics, management of insurance and specific driving related performance indicators.
What do we look for?
Negative
- Below average results in regulatory audits of fleet performance (where legislated) or in internal audits.
- No, or infrequent reviews of claims/loss/incident statistics and data.
- No specific targets to reduce numbers of incidents.
- Unco-ordinated approach to managing the fleet from a safety perspective.
Positive
- Regular reviews of crash data, fleet safety etc, with reports submitted to the Board or Senior Management.
- Cascaded responsibilities to departments or regions within the organisation.
- Higher “self-insurance” eg, higher excesses which encourages better internal incident prevention.
- Employees performance indicators and objectives include driving safety.
Risk improvement ideas
- Create measureable Objectives and Key Performance Indicators for Drivers, Teams/Divisions and the Company in respect of fleet safety, crash reduction etc.
- Establish regular reviews of claims data with your insurance broker, as well as non-insurance related crash data to establish trends, and identify suitable intervention measures.
- Seek approval from the Board, and submit analysis reports of a periodic basis.
- Involve the skills of Senior Departmental Management, Safety Officers and Fleet/Maintenance Managers.
- Encourage a suitable culture within the organisation to promote crash avoidance. Establish targeted loss reduction.
- Review your organisations “risk appetite” and review deductibles/excess, insurance cover etc.
As with all other aspects of employee safety, it is important that your business has documented Policies and Procedures to help manage the risks associated with the safety of employees when driving.
These Policies and Procedures will help create a Safe Driving Culture, as well as provide the basics for training and accountability throughout the business. Obviously, policies and procedures need to be periodically reviewed and updated.
What do we look for?
Negative
- No, or uncoordinated Safety Management Policies and Procedures for work-related driving.
- No Driver Safety Handbook.
- No specific vehicle preventative maintenance management.
- Ineffective or no incident reporting procedures.
- No risk specific guidance, policies or procedures, such as Drug/Alcohol Policy, Mobile Phone Use.
Positive
- Driving risks are included in Occupational Health & Safety Management and Committee Meetings.
- Processes exist to establish driving related policies and procedures.
- Regular reports to the Board on Safety matters, including driving risks.
- Formal reviews take place periodically on driving related safety policies and procedures.
Risk improvement ideas
- Establish driving-specific Safety Policies and Procedures, such as Mobile Phone Use, Fatigue Management, Drug/alcohol Policy etc.
- Periodically review all driving related safety policies and procedures.
- Ensure that driving safety is embedded within all other aspects of Occupational Health & Safety, such as Committee Meetings, Reports to the Board, Toolbox talks, Safety Communications to staff etc.
- Provide all drivers with a useful Drivers Safety Handbook.
Resources
Incidents (losses and near misses) are unique in that they provide us with real life opportunities to learn from our mistakes. Hence, incident investigation is critical in identifying causes of incidents, developing corrective actions and preventing reoccurrence.
However, incident investigation will prove fruitless unless the data gathered via incident reporting is accurate.
What do we look for?
Negative
- Reporting tools are lacking (e.g. no prompts, forms, cameras or on-board data systems provided in vehicles).
- Incident investigations focus entirely on insurance aspects and do not identify causes, determine preventability and / or develop corrective actions.
- Management reporting of overall motor fleet loss performance is sporadic / infrequent / not provided.
Positive
- Incident prompt / report forms and / or cameras or on-board data systems are provided in vehicles.
- Incident investigations are focussed on preventing reoccurrence and identify causes, determine preventability and develop corrective actions that are subsequently implemented.
- Management reviews of overall motor fleet loss performance are regularly and frequently conducted.
Risk improvement ideas
- Ensure that incident prompt / report forms are provided in all vehicles with all drivers informed of their use at induction.
- Ensure that an incident investigation form is established to facilitate these investigations with specific sections dedicated to causal analysis, preventability, corrective actions and follow-up / completion.
- Ensure that responsibility for facilitation of the incident investigation system is clearly appointed.
- Ensure that the Fleet Manager (or equivalent) conducts the investigation for all major crashes (with clear delineation of major and minor crashes).
- Provide training in incident investigation and root cause analysis (or equivalent) for the staff that will be conducting investigations.
- Share incident investigation reports and corrective actions with all drivers via team meetings.
- Include motor fleet loss performance reviews / reports in monthly management meetings.
Loss History refers to the frequency and average costs of past crashes, and is often used by Insurers to determine the acceptability and price of an insurance program. Past losses are an accurate statistical measurement of the exposure faced by a company, and how well they manage or control these exposures. When the frequency and average cost of incidents has an increasing trend, this would normally indicate that the management or controls are deteriorating or severely lacking. A decreasing trend usually indicates that management controls have improved.
What do we look for?
Negative
- High frequency (>20% of fleet) of motor vehicle losses.
- High severity (US$>20-<50k average cost) of motor vehicle losses.
- High frequency of driver "at fault" motor vehicle losses.
- No tracking / monitoring of motor fleet loss history at a management / organisational level.
Positive
- Loss lessons are used to create improvement opportunities.
- Individual Loss KPIs directly drive Individual performance plans which are tied directly tied to compensation.
- Low frequency of driver "at fault" motor vehicle losses.
- Well established tracking/monitoring of motor fleet loss history at a management/organisational level.
Risk improvement ideas
Establish tracking / monitoring of motor fleet loss history at a management / organisational level (i.e. for individual business units as well as the total organisation). As a start, key performance indicators to monitor are;
- Loss frequency (total number of losses per total number of vehicles in the fleet per annum)
- Average cost of loss (total cost of all losses divided by the total number of losses per annum)
- Driver at fault frequency (total number of driver at fault losses per total number of losses per annum)
- ‘Repeat offender’ losses (individual drivers with more than one loss over a rolling five year period)
For higher levels of tracking / monitoring all of these performance indicators should also consider kilometres / miles driven.
The extent and structure of expertise with regards to motor fleet risk management tends to directly determine the level of control that is employed to minimise motor vehicle losses.
A robust quality assurance system, when applied to fleet management systems, ensures continuity of these controls across all business units/operations.
What do we look for?
Negative
- The Fleet Safety Manager position is only part-time / shared with another role and filled by a relatively inexperienced person provided with poor support resources (e.g. is spread too thin).
- The Fleet Co-ordinator position merely manages assets and is not actively responsible for improving the motor vehicle loss performance.
- A Quality Assurance system is not established or is not applied to fleet management systems.
Positive
- A dedicated, experienced Fleet Risk Manager is appointed with appropriate support staff. This person is empowered to influence change and has direct Board support.
- The Fleet Risk Manager is ‘actively’ responsible for improving the loss performance of the fleet (i.e. not just insurance).
- ISO 9000 (or equivalent) QA system is established and applied to fleet management systems with regular audits and external certification.
Risk improvement ideas
- Irrespective of the title, ensure that the person responsible for the motor fleet activities is experienced in various motor fleet controls and tools (and if necessary given the business size, supported by staff with good knowledge of day to day operations). This person should be made ‘actively’ responsible for improving the loss performance of the fleet and not just liaising between the company and the insurer.
- Establish a rigorous Quality Assurance system across all operations of your business (including fleet management) with regular internal / external audits and external certification.
According to research, drivers who use mobile phones whilst driving, hands-free or not, are up to four times more likely to be involved in a collision. Some studies have equated using a mobile phone to being twice over the drink drive limit. In many countries, using a mobile phone ‘to your ear’ whilst driving is prohibited by law, but there the Police can prosecute drivers whilst ‘hands-free’, by other road traffic legislation, citing ‘unsafe driving’ as the offence.
Whilst truck drivers need to use a range of technology in a modern day truck, they also need to be aware of the risk of distraction. Unnecessary communication via two-way radio, CB, mobile phone etc should be avoided, unless the truck is parked up. GPS devices should be programmed at the start of the journey, and if modifications are needed, the driver should pull over safely to do so.
What do we look for?
Negative
- Drivers are allowed to use phones, radios and other equipment whilst driving without any control or training regarding the dangers of doing so.
- Companies do not supply hands-free kits in truck cabs.
- Companies do not monitor company owned mobile phone records to check on validity and duration of calls.
Positive
- Policies are in place to reduce the risk of driver distraction when driving.
- Hands-Free kits are used for all mobile phones.
- Drivers are instructed and trained to avoid unnecessary use of telematics and communication devices when driving.
- Company monitors the use of in-cab equipment.
Risk improvement ideas
- Train driving and non-driving staff of the dangers of distraction when driving. Office based staff (e.g. dispatchers) are trained to call drivers only when necessary, and to keep calls short and to ensure the driver is talking “hands-free”.
- Create procedures that require drivers to program telematic devices (such as SatNav, GPS etc) at the start of the journey, or during rest breaks. If these systems need to be modified en route, ensure the drivers pull over when safe to do so, and make the necessary adjustments.
- Discourage unmerited communication by two-way radio, mobile phone etc. Monitor drivers at scheduled rest breaks, not when driving. Audit phone records periodically at randomly to check if drivers are using phones when driving.
No matter how long or short a route may be, being prepared is a significant factor in risk reduction. By planning a route, companies and their drivers will be able to predict hazardous aspects of road design, approach to customers premises etc. Alternative, safer routes and times may be considered and thus potentially avoid incidents.
What do we look for?
Negative
- Route planning is not part of normal trip scheduling.
- Companies Drivers are left to determine the approach to destinations.
- Many of the delivery sites are Hazardous Sites (e.g. Fuel Depots).
- Routes are travelled infrequently.
Positive
- Route Plans are developed for all trips by experienced dispatchers or drivers.
- Delivery sites all have good access and egress, and have one-way systems on site.
- Good communication between dispatcher and driver.
- Sat-Nav or GPS is used to assist drivers on route.
- Majority of routes are frequently used.
Risk improvement ideas
- Consider developing safe, predetermined route plans for frequent routes. Communicate these to drivers or utilise GPS systems with pre-determined routes programmed in.
- Ensure that one-off routes are evaluated for hazardous road features, speed limits etc. Hazards may include: built up areas, schools, hospitals that are passed on route.
- If required to deliver to hazardous sites, ensure there are at least well-developed access and egress plans.
- Complete a risk assessment for each route, taking into consideration commodities, familiarity, access/egress, and number of alternative routes.